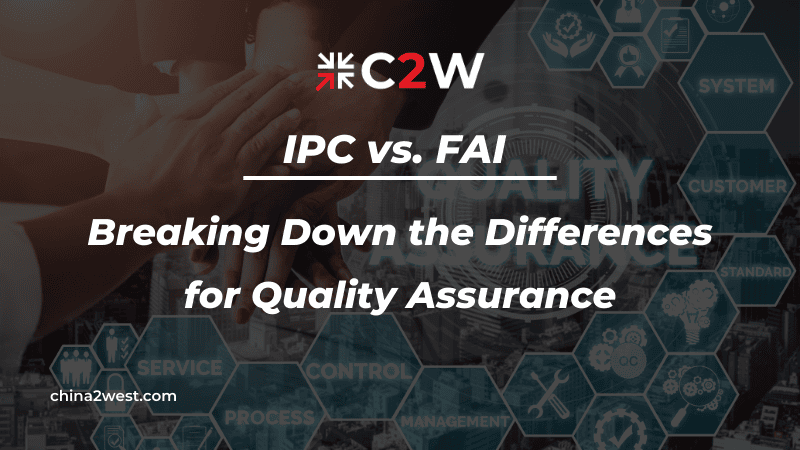
Quality assurance is paramount in the manufacturing sector, ensuring that products meet stringent standards before reaching the market. Among the methodologies used to maintain these standards, IPC (Initial Production Check) and FAI (First Article Inspection) stand out as critical processes. Understanding the differences between these two approaches is essential for manufacturers looking to enhance their quality assurance practices. This blog will explore IPC and FAI, their significance, and how they can be effectively implemented.
Initial Production Check (IPC)
IPC is a quality control process that occurs at the beginning of the production phase. It involves the inspection of the first batch of manufactured products to ensure that the production line is set up correctly and that the products meet the design specifications and quality standards. IPC is mainly about evaluating the production process and the initial outputs to make necessary adjustments before the bulk of production proceeds. It helps in identifying any issues that could affect product quality early in the production process, thus avoiding large-scale defects.
Lear more about Initial Production Check here
First Article Inspection (FAI)
FAI, on the other hand, is a more detailed and often more technical process that occurs before the full production begins. It typically involves a comprehensive examination of the very first sample product or part from a production line to verify that all engineering, design, and specification requirements are met. FAI is crucial in industries where products must adhere strictly to safety, regulatory, and quality standards. This inspection is documented thoroughly to ensure that every aspect of the design has been achieved correctly before mass production is authorized.
Read more about First Article Inspection here
Key Differences Between IPC and FAI
Both IPC and FAI are crucial in quality assurance processes but are distinct in their purpose, scope, timing, detail level, and industry application. Understanding these differences can help manufacturers better implement quality controls tailored to their production needs.
Focus Areas
Initial Production Check primarily examines the conformity of raw materials, components, and initial production techniques to the pre-approved specifications. It assesses whether the assembly line is set up correctly and if the initial outputs adhere to quality standards. IPC can also involve checking the machinery and processes to ensure everything functions as intended.
FAI is more comprehensive in that it not only checks the product against specifications but also verifies all documentation, design specifications, and engineering requirements. It is a meticulous process where every aspect of the first product is compared to the design files and blueprints to ensure absolute accuracy and completeness.
Timing in the Production Cycle
The timing of IPC and FAI is a significant differentiator between the two processes. IPC occurs before mass production starts, during the early production stages. This timing allows manufacturers to address any issues that may arise from the setup, tooling, or materials used in production. By identifying and correcting these problems early on, manufacturers can reduce waste, save time, and lower production costs.
Conversely, FAI takes place after the first batch of products is produced. It assesses whether the production process can consistently produce items that meet the required specifications. FAI provides manufacturers with a final verification before large-scale production, ensuring that the processes and tooling used are capable of delivering quality products consistently.
Industry Application
IPC is commonly used in industries where the quality of raw materials significantly impacts the final product, such as electronics, textiles, and construction materials.
FAI is widely utilized in precision engineering sectors, such as aerospace, automotive, and electronics, where adherence to design specifications is critical for the functionality of the final product.
Documentation and Compliance
Documentation plays a crucial role in both IPC and FAI, but the nature of the documentation differs. IPC may require basic records of inspection results, including any non-conformities and corrective actions taken during the production process. This documentation is essential for ensuring that any issues are addressed promptly and do not recur.
In contrast, FAI requires a more extensive documentation package, often including detailed reports, drawings, and specifications. This documentation serves as a formal record of the first article’s compliance with the required standards. FAI documentation is often submitted to clients or regulatory bodies to demonstrate adherence to quality assurance practices, making it an essential aspect of product reliability and trust.
Impact on Quality Assurance Strategy
Both IPC and FAI contribute significantly to an effective quality assurance strategy, but they do so in different ways. IPC is invaluable for early problem detection and prevention, allowing manufacturers to make necessary adjustments before mass production. This proactive approach not only enhances product quality but also fosters a culture of continuous improvement within the manufacturing process.
On the other hand, FAI serves as a critical checkpoint that validates the entire production process. It ensures that the systems and procedures are in place to consistently produce high-quality products. By successfully completing FAI, manufacturers can gain confidence in their production capabilities, facilitating smoother operations and increased customer satisfaction.
Conclusion
Both the Initial Production Check and First Article Inspection are essential components of a robust quality assurance framework. While they serve different purposes and occur at different stages of production, their ultimate goal is the same: to ensure that products meet the highest quality standards. Understanding the differences between IPC and FAI allows manufacturers to implement effective quality control measures that can significantly impact overall production success.
For more insights into quality control and quality assurance practices and to discuss how we can assist you in implementing product control and assurance in your production process, contact us today. Our team of experts is here to help you optimize your quality assurance practices for maximum effectiveness.